Introduced in Europe in the 17th century, caning was a popular method for chair seating. Rattan—a plant native to Southeast Asia—was harvested, cut, and woven to create strong seats and chair backs.
The techniques and materials have not changed much in all the years and only a few common tools are necessary to repair chair seats, making chair caning a craft that nearly anyone can master with just a little patience and tenacity. The strands of cane used in chair seat weaving is the shiny, glossy skin or inner bark from the stem or trunk of the rattan palm, genus Calamus Rotan. There are hundreds of species, but only a few are suited to produce the high quality needed for chair seat weaving.
Chair cane (the outer skin or bark of the rattan palm) is used primarily in weaving antique and modern chair seats. However, it’s also used extensively as wrappings on rattan furniture and is sometimes used to weave entire sets of new or reproduction wicker furniture.
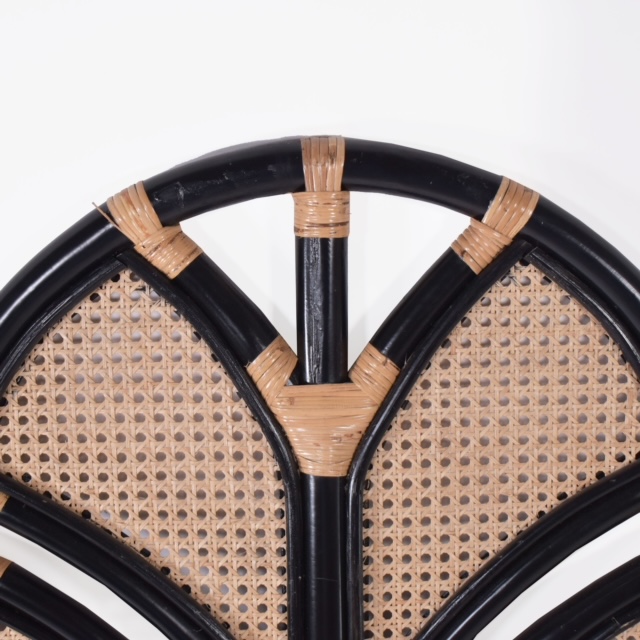
Here’s an example of the hole-to-hole Caning , traditional hand caning, or lace cane seat which is weaving individual strips through a series of drilled holes around the perimeter of the chair seat frame. The result ends in an octagon shape pattern throughout the seat.
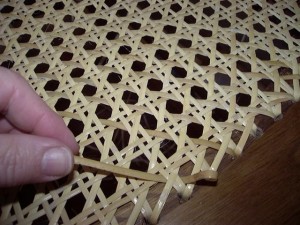
Here is an example of a wide binding cane seat, porch cane or binder cane seat, where the wide binding cane strands are woven around the seat frame rungs both top and bottom creating a double layer of cane. Frequently the design on the top of a stool or chair seat would be in a diamond pattern with a simple twill or herringbone pattern on the bottom or back. This type of chair seat pattern using this material was/is very popular with chairs and rockers used outside on a porch, hence the name, “porch cane seat.”
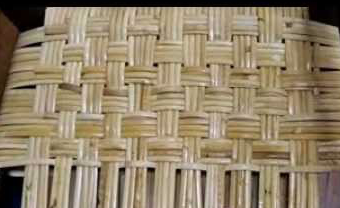
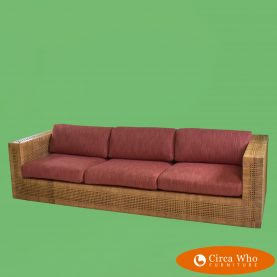
Here is an example of spline machine or cane webbing, where a pre-woven sheet of cane is inserted into a groove around the perimeter of the chair seat and held in place with glue and reed spline.
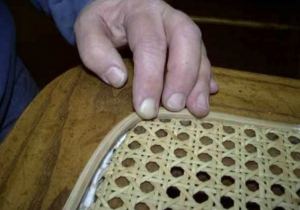
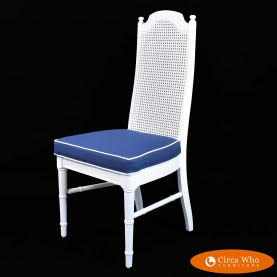